Copachisa
Optimizing supply chains for construction
01
The
Challenge
Copachisa, as a leader in the construction industry, faced challenges related to the efficient management of supply chains across multiple construction sites, as did the industry as a whole.
These challenges impacted the timely delivery of essential materials and, consequently, construction schedules.
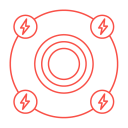
Pain points
Lack of visibility: Difficulty monitoring the status and deliveries of supplies in real time.
Manual and disconnected processes: Lack of data integration caused operational bottlenecks.
Reactive incident management: Supply issues were identified late, affecting project timelines.
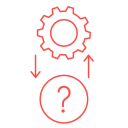
Root causes
Non-integrated systems for inventory and schedule management.
Reliance on manual communication between construction teams and suppliers.
Disconnect between BIM models, project managers, site, and contractors.
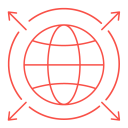
Business impact
Increased costs due to construction delays and downtime.
Increased pressure on teams to adjust schedules and optimize deliverables.
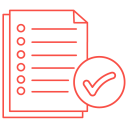
Desired outcome
A centralized platform that would provide full supply chain visibility, automate incident management and enable real-time collaboration between internal teams and suppliers.
02
The Result
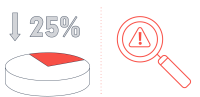
25% reduction in critical supply delays, thanks to early detection of risks.
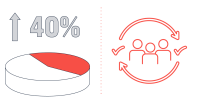
40% improvement in collaboration between internal teams and suppliers.
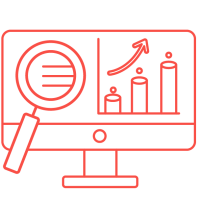
Increased visibility and control: Real-time monitoring of key deliverables.
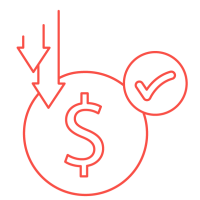
Reduced delay costs: Less reliance on costly recovery measures.
03
Our Role
Our role in development
- Joint collaboration: As co-owners of the product, we work closely with Copachisa to define key requirements.
- Data integration: We incorporate information from project planning to supply monitoring within Copachisa and integrated with their contractors through Chatbots.
- Alert automation: We develop automated workflows to manage incidents and minimize disruptions.
Key processes
- Initial mapping of supply chain processes.
- Platform design and development in agile iterations.
- Testing and early involvement in the use of the system.
04
The Solution
We developed and implemented a customized supply chain management web platform and a set of chatbots that provide:
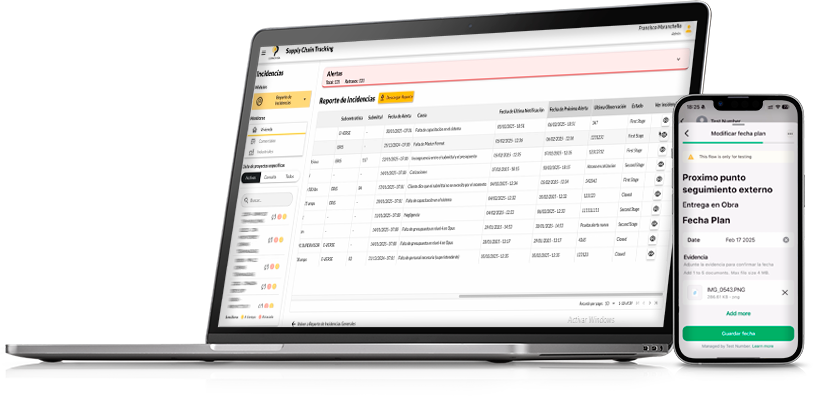
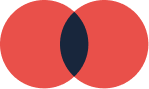
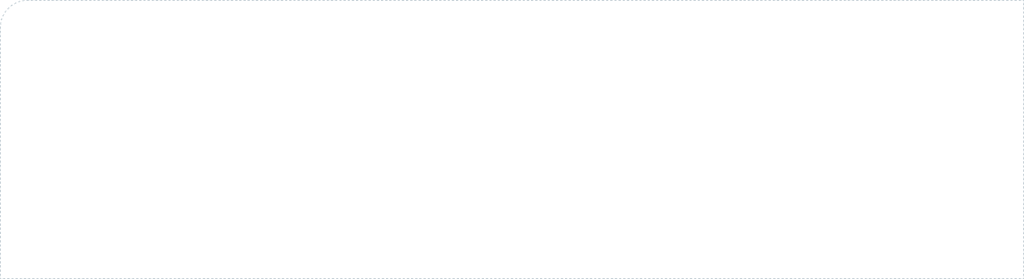
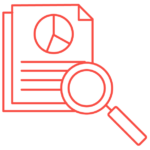
Proactive monitoring of critical deliveries: Enables early detection of delays and corrective action.
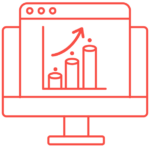
Real-time data dashboards: Provides clear visibility for all stakeholders.
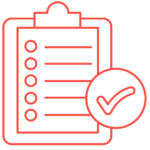
Incident handling automation: Issues are automatically logged and tasks are assigned for resolution.
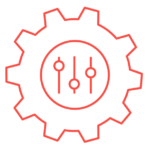
Customization of escalation matrices: Customization of actionables, steps, and taskers for each cause and issue occurrence throughout the entire project lifecycle.
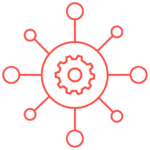
Integration with existing systems: We leverage data from internal and external sources to improve decision making.
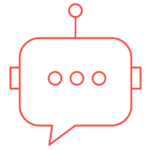
Integration with the entire supply chain throughout the project: We integrated with Copachisa’s internal ERP, Autodesk’s ACC, and with each contractor through WhatsApp chatbots.
05
Key Results
This solution not only solved Copachisa’s challenges, but became an adaptable SaaS-like product for other industry players.
06
Who's
the Client?
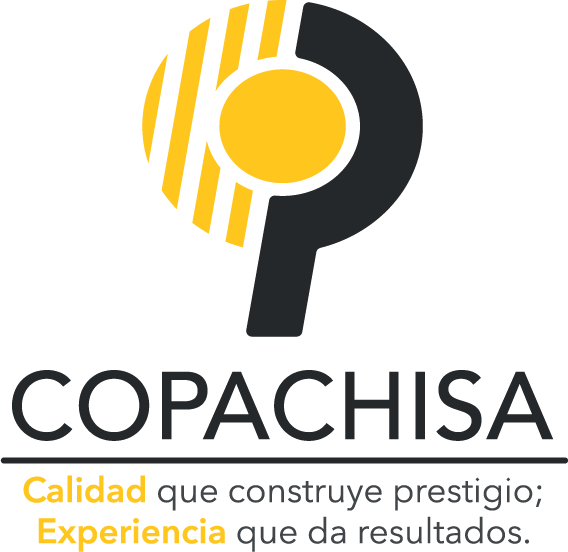
Copachisa is a leading Mexican construction and project management company, known for executing large industrial, commercial and infrastructure projects.
With more than 50 years of experience, it is recognized for its focus on innovation and the delivery of high quality projects in tight deadlines.
A Few Words from Our Partner
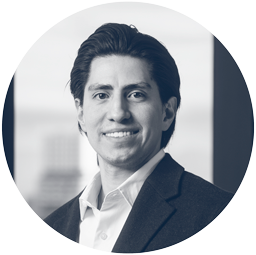